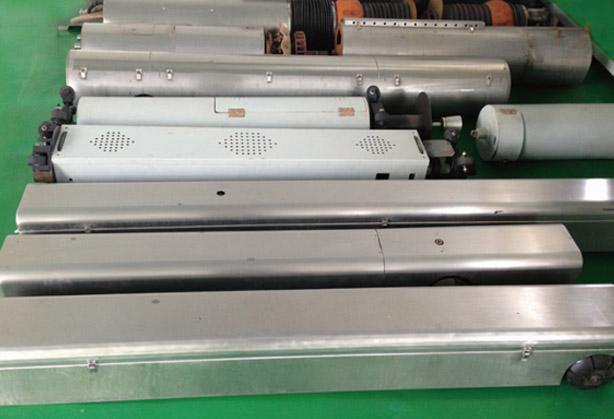
针对 管道内壁检测及焊口防腐,大仓开发了补口及检测机器人技术:
1 - 抛丸除锈机器人2 - 钢丝击打除锈机器人3 - 焊口清理机器人4 - 内喷涂(环氧粉末/液体涂料)补口机器人5 - 内防腐检测机器人
1 - 储罐、船舶探伤检测机器人2 - 储罐、船舶除锈防腐机器人
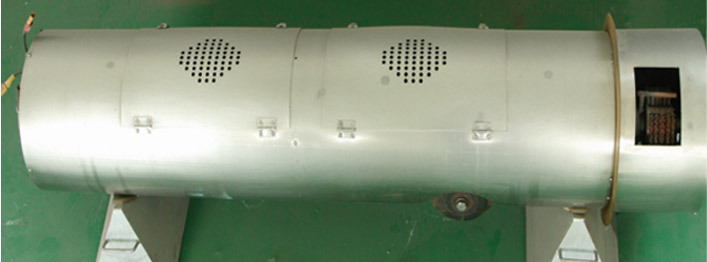
钢丝击打除锈机器人
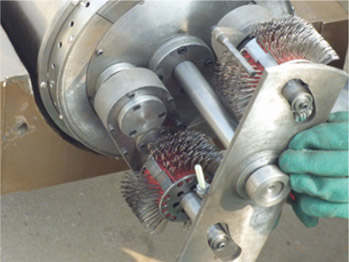
钢丝击打除锈机器人
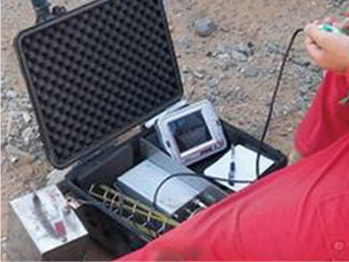
机器人遥控系统
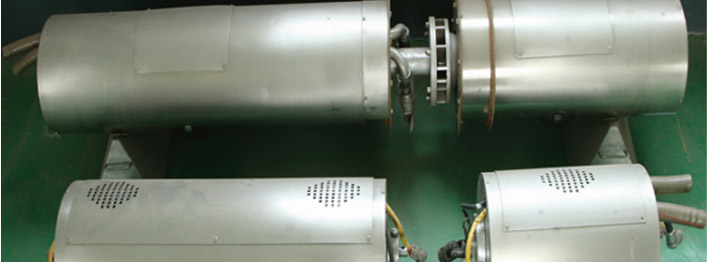
抛丸除锈机器人
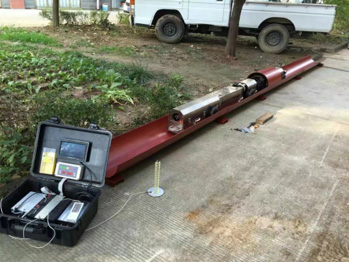
管道内补口机器人
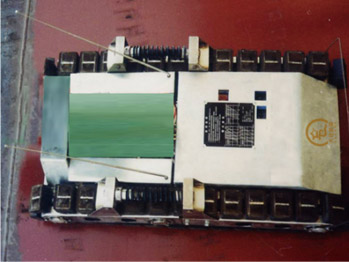
储罐检测机器人
酸 洗
随着管道防腐工艺的深入发展,近年来管道在防腐前酸洗,越来越引起国内外用户的重视。尤其是国外防腐工程中,钢管防腐生产线酸洗工艺是必备的。为满足国内外用户对管道防腐质量提升的不断要求,青岛大仓防腐有限公司用了三年多的时间,组织研发了钢管外表面在线酸洗装置。形成了从生产纯水-配药-酸洗-水洗-风干-酸雾净化-废水净化再循环利用-达标排放一整套的完整体系。为实现钢管外表面在线酸洗提供技术、装备支撑。
适应管径范围广,生产效率高。
选用磷酸清洗液,减少对人体的伤害和对环境的污染。
废液可实现回收和重复利用。同时也可以实现达标排放。
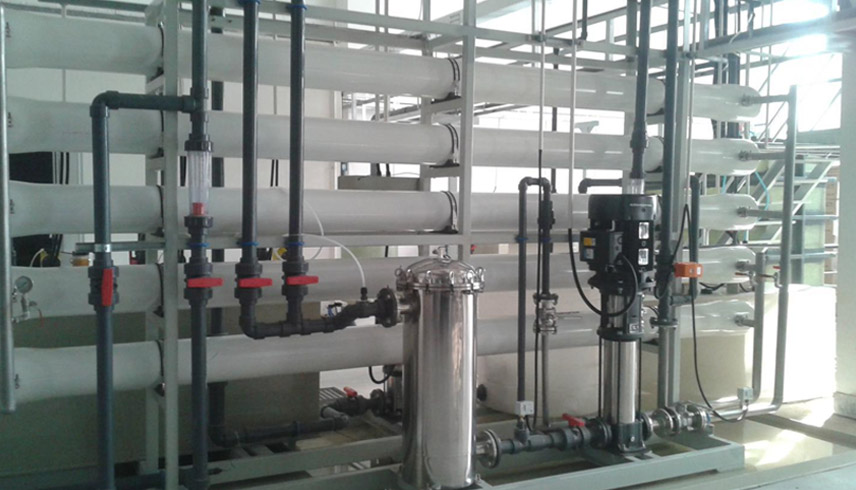
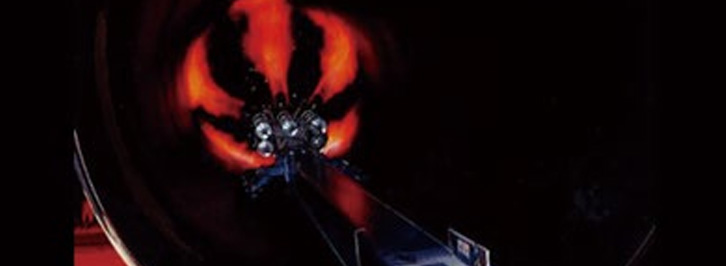
功能:除钢管表面水分和油渍,将钢管表面加热至所需温度
构成:火焰分布器、燃气管路系统、助燃风机、移动系统、电控柜。
工作原理:用天然气燃烧器对除锈前的钢管进行预热。支撑杆 前端的燃烧头伸入管内,火焰直接对着管壁进行加热,钢管在加热 过程中保持旋转,确保加热均匀,钢管两端分别设置密封室,确保 加热过程中火焰不外逸。密封室顶部安装通风口及通风机,燃烧过 程产生的烟气通过通风管道排出室外。
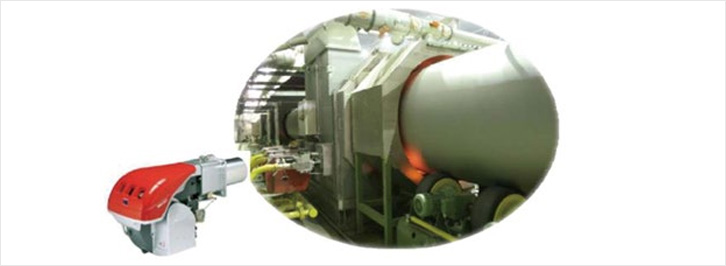
功能:对钢管表面进行预热。
该系统主要由燃烧器、预热炉、烟囱、电控柜等组成。工作原 理是钢管预热过程中 , 燃烧器火焰采用从管底加热、沿管体旋转上 升的方式,使热量充分利用。
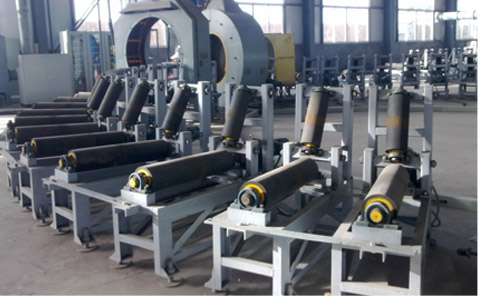
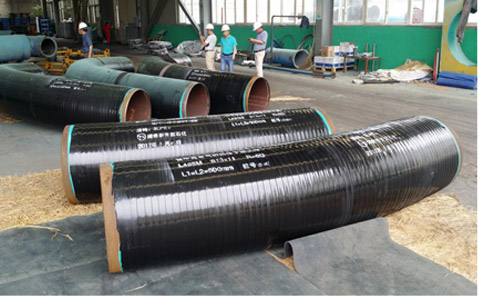
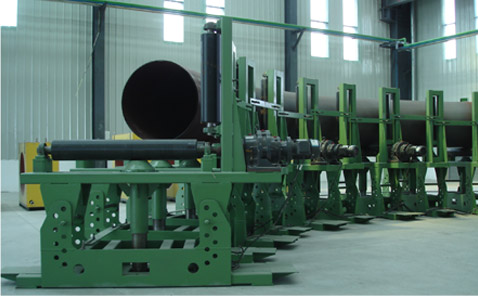
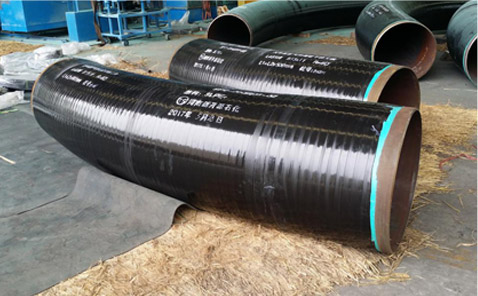
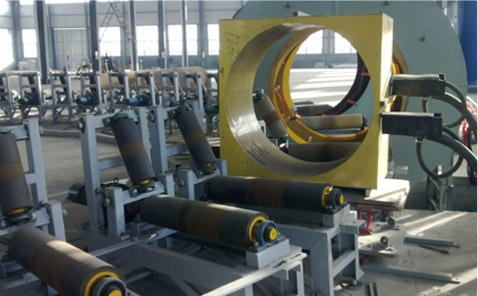
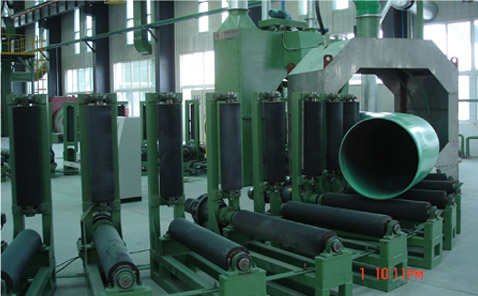
该全新工艺,可在同一条作业线上实现该全新工艺,可在同一条作业线上实现钢管除锈、防腐、保温的综合效果,并进行强化处理,使防腐层、保温层、粘结层、保护层的四层结构更可靠。
钢管除锈 液体或环氧粉末防腐
保温层发泡
共聚物胶热缠绕
聚乙烯热缠绕
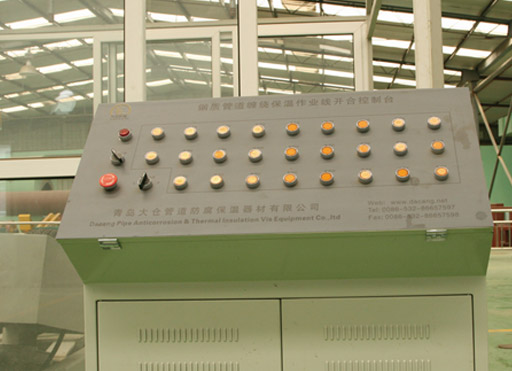
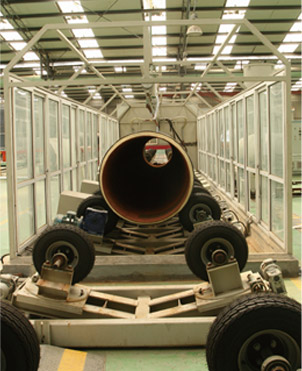
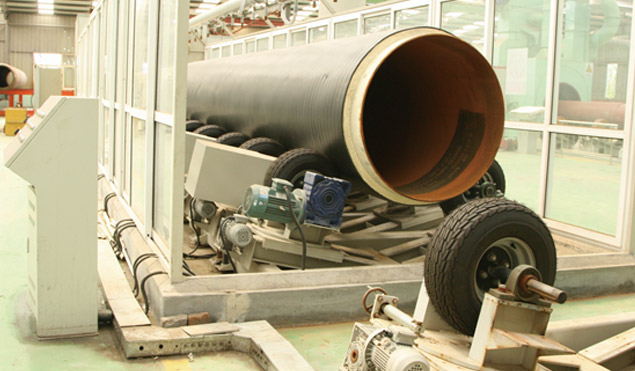
- 1
发泡、缠胶、缠绕PE保护层,一次完成。工艺顺畅,可实现自动化生产,节约人工,节约时间,易于操作。避免了过去二步法生产经常出现的安全问题。
- 2
基层使用液体或环氧粉末防腐,使钢管表面防腐蚀性能加强。万一出现保温层局部渗水,水与聚氨酯产生的酸性介质也不能对钢管表面产生腐蚀。
- 3
用共聚物胶来粘接泡沫层与PE保护层,使其结合更加牢固。从而保证多层工艺的完整性和同步可靠性,解决了过去的脱壳问题和由于夹克层的伸缩使补口拉坏进水问题。即使出现了聚乙烯外护层破损现象, 也不会穿线。
- 4
新工艺采用喷涂发泡,泡孔均匀并充分固化、硬化。发泡质量全程可视,产生的气体可自由释放,不会形成絮状物和管内气泡。
- 5
采用热缠绕工艺完成的共聚物胶5、采用热缠绕工艺完成的共聚物胶层和聚乙烯层,把原来的轴向拉伸成型改成现在的径向拉伸成型,改变了外护层PE的分子结构方向,有效克服了PE层与保温层脱壳的问题。
- 6
新工艺自动作业线调节简单方便,发泡层厚度和PE层厚度可轻松调整。生产过程不需更换模具,在一条作业线上多种口径(中426至中1620)、多种厚度的保温管制作都可以完成,而且更适合大口径管。
- 7
由于采用缠绕工艺,不需要把夹克层做得太厚,可节省聚乙烯材料。自由发泡过程较老工艺也不会形成2- 3mm的硬壳,可节省聚氨酯材料。
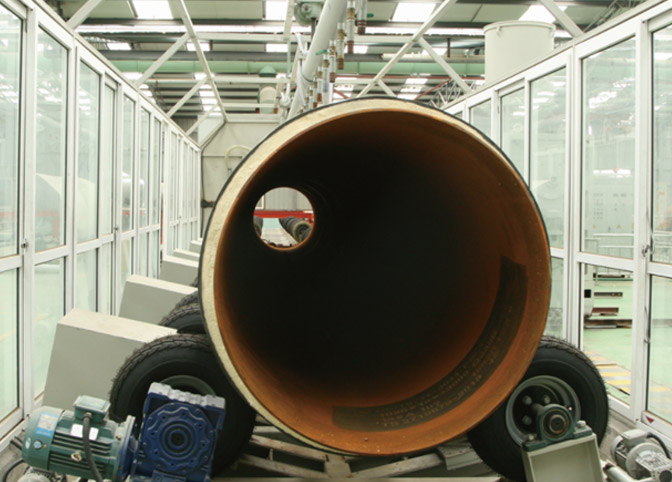
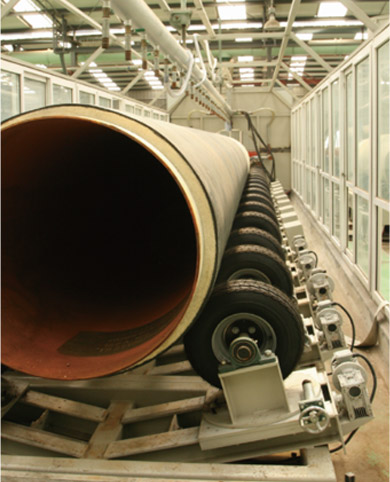
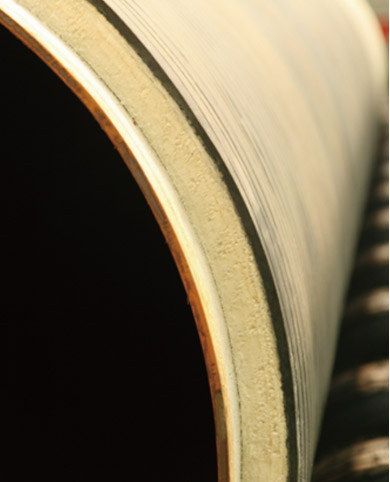
管道内环氧粉末喷涂技术,由于受制于高压静电喷涂方式,目前市场普遍采用的是文丘里泵喷涂工艺,上粉率一直徘徊在50%左右,尤其是直径大于500毫米钢管就更低。粉末回收量大,溢粉严重。为了改变 现状,满足国内外用户对上粉率不断提升的追求,青岛大仓防腐有限公司用了近两年时间,成功的研发了新一代管道内环氧粉末喷涂技术,上粉率高达95%。技术创新、工艺上突破,为新一代管道内环氧粉末 喷涂技术提供有力支撑。
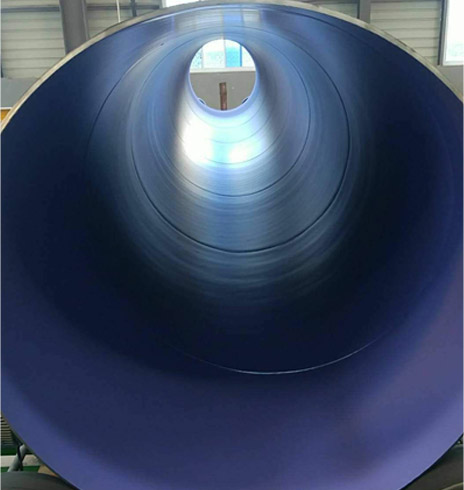
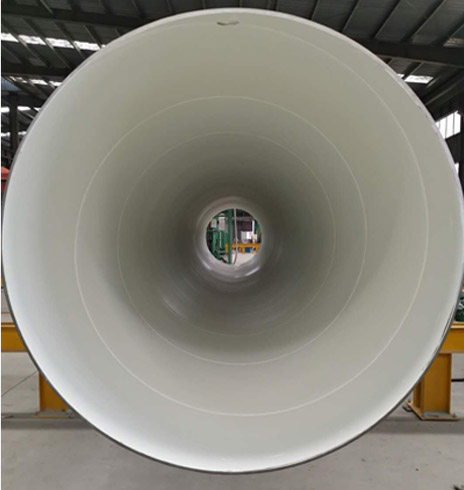
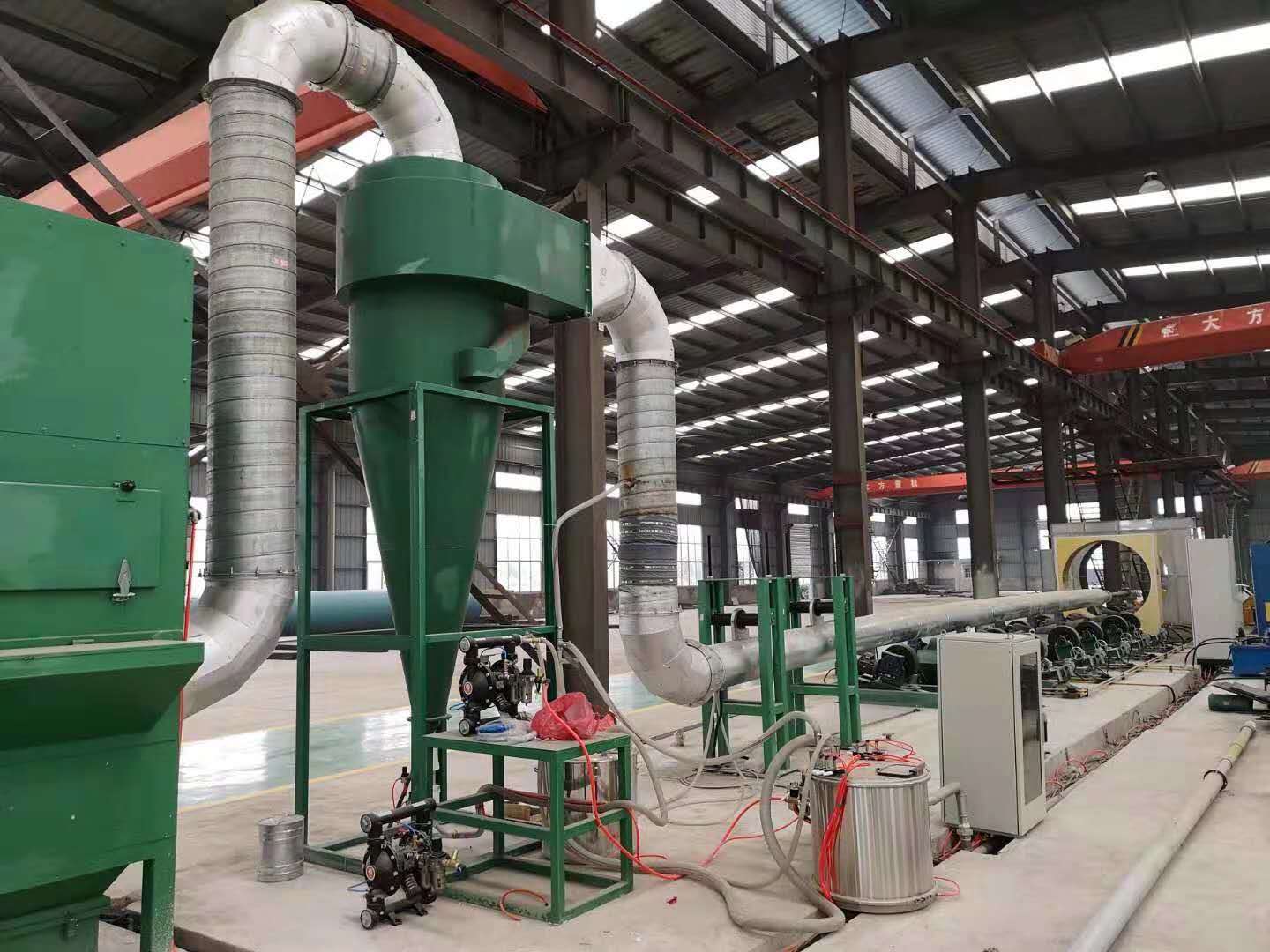
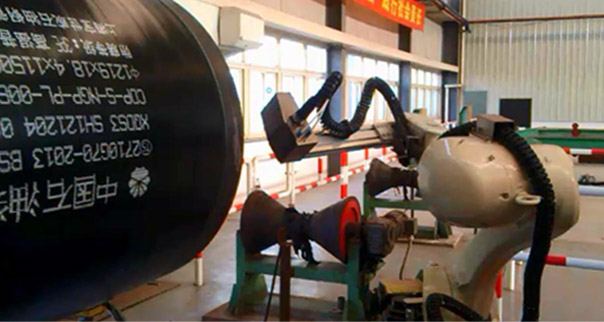
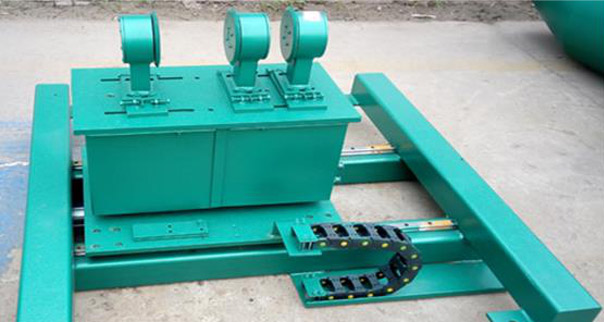
为顺应科学和技术发展,提高钢管防腐生产线的生产效率和质量、降低生产成本、减少操作人员数量、增强安全性,我公司研发了全自动钢管防腐生产线。
全自动钢管防腐生产线是对目前广泛使用的钢管防腐生产线模式进行的革命性升级、创新和发展。该全自动生产线将传统的生产线的机械性能进行全面提升、改进、完善,在此基础上增加全新的钢管防腐生产自动控制系统(ACSOSAP),实现钢管防腐生产线全自动化生产。
钢管防腐生产自动控制系统(ACSOSAP)由工控机(PC)、工业可编程控制器(PLC)、触摸屏(HIM)、变频器、工业以太网、SCADA组态软件、模块化生产线自动控制软件组成。实现对钢管的内外除锈工艺生产线、3PE工艺生产线、内外FBE工艺生产线、内外喷漆工艺生产线、裸管上线、成品管下线、半成品转移、酸洗钝化、喷标、在线检测等自动控制。
钢管防腐生产自动控制系统(ACSOSAP)主要分两个层:车间监控层和现场设备层。
车间监控层实现车间级设备的监控,其包括生产设备状态的在线监控、设备故障报警及维护、生产统计、生产调度、数据分析及预警、生产信息储存及上传等。该层主要由工控机(PC)、工业可编程控制器(PLC)、SCADA组态软件、工业以太网组成。
现场设备层实现主要连接现场生产线的设备,例如分布式 I/O、驱动器、执行机构、传感器、智能仪表等。完成现场生产线的设备的工艺控制和连锁控制,以及现场生产线的设备运行状态及生产信息的采集和上传。该层主要由工业可编程控制器(PLC)、触摸屏(HIM)、变频器、模块化控制软件组成。
以往的防腐作业线,在加工处理不同口径的管道时,需要经常在不同尺寸的管道传送装置之间以人力转换。既费事,又费时,安全性也会受影响。该新型专利技术,在传送运行时可自动切换开合尺寸,而不必进行人工转换。
因此,具有以下突出优点:
1、自动化程度高,大大提高生产效率;
2、大大降低工人的劳动强度,并提高了安全性。
3、长期使用,传送轮磨损均匀,传送稳定,保障防腐质量。
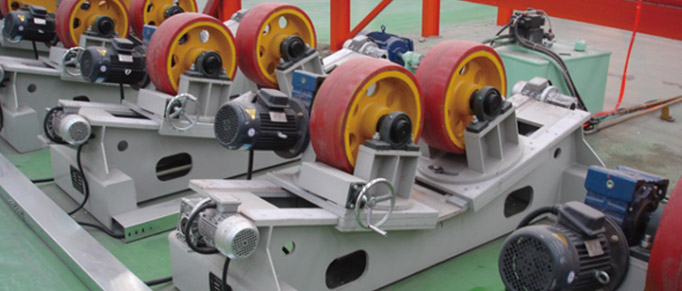
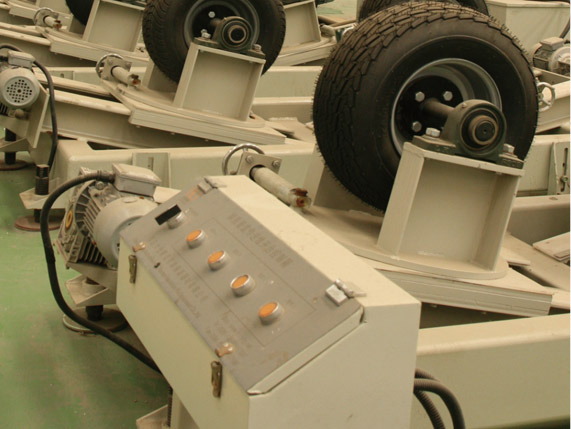
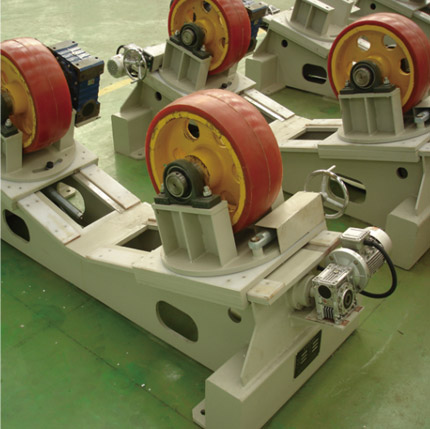

我们的专利产品。适用于多种口径钢管的多管同时除锈及内外防腐作业,大大提高了生产效率,降低了成本。
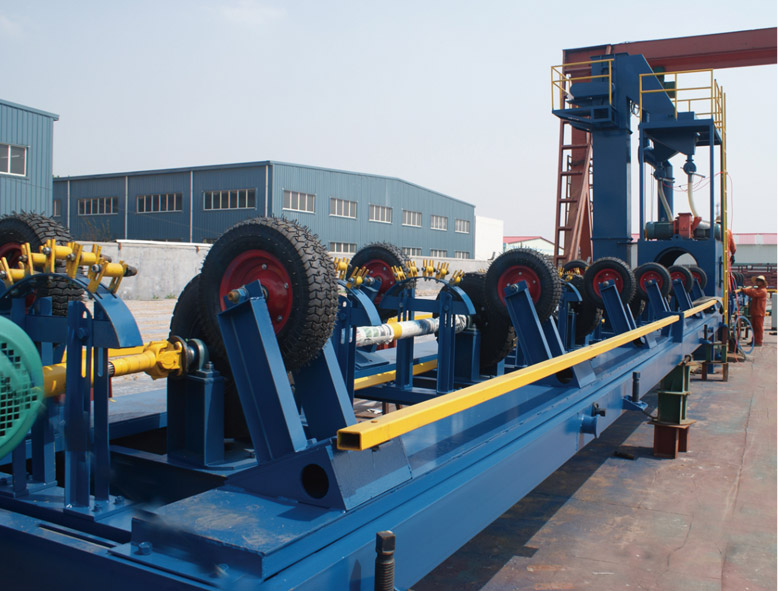
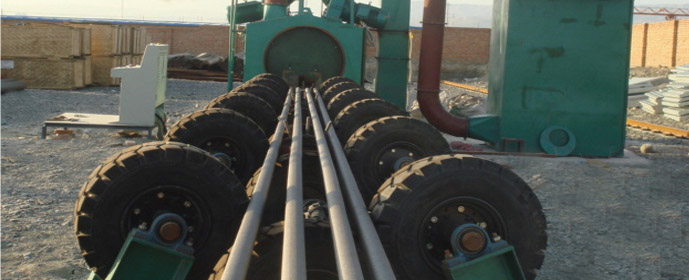
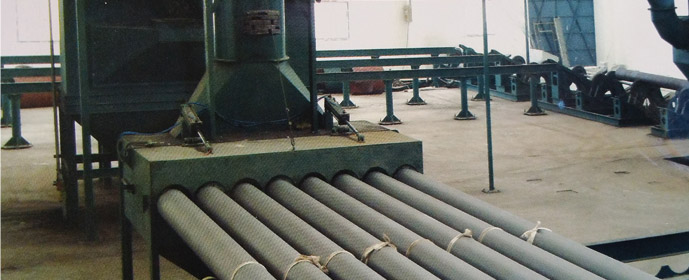